Prolonging Lifespan of Industrial Pumps: Expert Repair and Maintenance Services
By:Admin
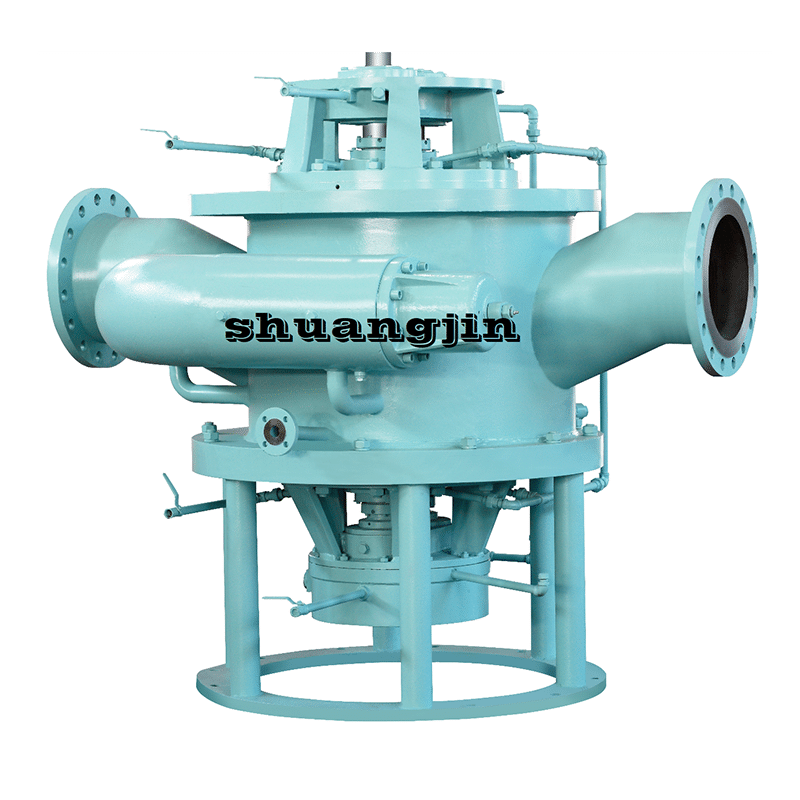
With over 25 years of industry experience, Industrial Pump Repair specializes in repairing, rebuilding and maintaining all types of industrial pumps, including centrifugal, positive displacement, reciprocating, and more. The team of experienced technicians at the company are equipped with the latest tools and expertise to deliver precise and efficient pump repair services tailored to the specific needs of each customer.
"We understand that any downtime due to malfunctioning equipment can have a significant impact on a business's operations and profitability, which is why we prioritize our customers' needs and work tirelessly to deliver fast, reliable and cost-effective solutions," said a representative from Industrial Pump Repair.
The company takes pride in their commitment to quality workmanship and customer satisfaction. They offer a variety of services to help keep industrial pumps running smoothly, including preventative maintenance programs, pump inspections, vibration analysis, laser alignment, and performance testing, to name a few.
One of the key advantages of working with Industrial Pump Repair is their capability to provide on-site services. Their experienced technicians can travel to clients' facilities to diagnose and repair issues on-site, ensuring minimal disruption to their operations. They also carry a wide range of spare parts and components to minimize the time needed for repairs.
In addition to their repair and maintenance services, Industrial Pump Repair offers top-of-the-line replacement pumps and parts from industry-leading manufacturers such as (need remove brand name). They provide installation and commissioning services to ensure that their clients' new pumps are installed correctly and work reliably for years.
The company is committed to building long-term partnerships with their clients. They take the time to understand each client's distinct requirements and tailor their services to meet their unique needs. By providing comprehensive services that encompass every aspect of industrial pump repair and maintenance, they empower their clients to minimize their downtime, optimize their equipment's performance, and save on costs.
In conclusion, Industrial Pump Repair is a trusted partner for businesses seeking to improve the reliability, performance, and efficiency of their industrial pumps. Their extensive expertise, commitment to quality workmanship, and customized services have made them a top choice among businesses in need of pump repair and maintenance services. Contact them today to experience their exceptional services and discover how they can help take your business operations to new heights.
Company News & Blog
Prolonging Lifespan of Industrial Pumps: Expert Repair and Maintenance Services
Industrial Pump Repair, a reliable provider of high-quality industrial pump services, is proud to announce their commitment to helping businesses improve the performance and reliability of their pumps. The company specializes in providing comprehensive pump repair and maintenance services to ensure that businesses can operate at peak efficiency in every aspect of their operations.With over 25 years of industry experience, Industrial Pump Repair specializes in repairing, rebuilding and maintaining all types of industrial pumps, including centrifugal, positive displacement, reciprocating, and more. The team of experienced technicians at the company are equipped with the latest tools and expertise to deliver precise and efficient pump repair services tailored to the specific needs of each customer."We understand that any downtime due to malfunctioning equipment can have a significant impact on a business's operations and profitability, which is why we prioritize our customers' needs and work tirelessly to deliver fast, reliable and cost-effective solutions," said a representative from Industrial Pump Repair.The company takes pride in their commitment to quality workmanship and customer satisfaction. They offer a variety of services to help keep industrial pumps running smoothly, including preventative maintenance programs, pump inspections, vibration analysis, laser alignment, and performance testing, to name a few.One of the key advantages of working with Industrial Pump Repair is their capability to provide on-site services. Their experienced technicians can travel to clients' facilities to diagnose and repair issues on-site, ensuring minimal disruption to their operations. They also carry a wide range of spare parts and components to minimize the time needed for repairs.In addition to their repair and maintenance services, Industrial Pump Repair offers top-of-the-line replacement pumps and parts from industry-leading manufacturers such as (need remove brand name). They provide installation and commissioning services to ensure that their clients' new pumps are installed correctly and work reliably for years.The company is committed to building long-term partnerships with their clients. They take the time to understand each client's distinct requirements and tailor their services to meet their unique needs. By providing comprehensive services that encompass every aspect of industrial pump repair and maintenance, they empower their clients to minimize their downtime, optimize their equipment's performance, and save on costs.In conclusion, Industrial Pump Repair is a trusted partner for businesses seeking to improve the reliability, performance, and efficiency of their industrial pumps. Their extensive expertise, commitment to quality workmanship, and customized services have made them a top choice among businesses in need of pump repair and maintenance services. Contact them today to experience their exceptional services and discover how they can help take your business operations to new heights.
10 Essential Applications of Screw Pumps in Various Industries
The Use of Screw Pump: Understanding the Importance in Industrial ApplicationsScrew pumps have been around for a while and used in industrial applications for various reasons. They have become popular because of their efficiency and versatility, with many companies using it for different purposes. These pumps can be found in oil and gas industries, food-processing plants, petrochemical plants, and many more.Screw pumps work by moving fluid inside their chambers. A helical screw rotates inside a cylinder, creating pressure that forces fluid to flow through the pump. As it moves, it also moves pockets of fluid along the way, which reduces pulsation, ensures smooth continuous flow, and maximizes efficiency.Thanks to screw pumps, manufacturers can efficiently move liquids without disturbing the medium's temperature, density, or viscosity. It's perfect for transferring both low and high viscosity liquids, making it the perfect solution for moving anything from crude oil to food products.This pump is versatile, cost-effective, and often replaceable. However, like any machinery, there are advantages and disadvantages to using a screw pump. Below, we'll take a look at some of the benefits of using screw pumps in your system.Advantages of Screw Pumps1. Low Maintenance RequirementsOne of the primary advantages of using a screw pump is that it requires minimal maintenance. The low maintenance requirements of screw pumps make it cost-effective, and you will save a considerable amount of money in maintenance and repairs.2. Efficient PerformanceScrew pumps are designed for maximum efficiency. They can handle high and low viscosity liquids, making it easy to move anything from crude oil to food products. Their design optimizes the flow of liquid, reducing pulsations and ensuring smooth, continuous flow.3. High Suction CapabilityScrew pumps can handle high suction, making it easy to transfer liquids of different viscosities. They can handle everything from light fuel oils to heavy crude oil.4. Can Handle Multiple ViscositiesScrew pumps are suitable for transferring liquids of different viscosities. They are often used in the oil and gas industry, where they can be used to transfer crude oil, diesel fuel, and heavy oil.5. They Are VersatileScrew pumps are highly versatile. They are used in a variety of industries for many different purposes, making them ideal for any application that requires the movement of liquids.6. Reduced Noise LevelScrew pumps are relatively quiet, making them ideal for indoor settings where noise levels need to be kept to a minimum.How to Select the Right Screw PumpSelecting the right screw pump is essential to ensure that you get the desired results. The best way to select the right screw pump is to work with a reputable and experienced manufacturer. When selecting a screw pump, you need to consider factors such as:1. The Viscosity of the LiquidThe viscosity of the liquid you are transferring is a crucial factor when selecting a screw pump. You need to ensure that the pump you choose can handle the viscosity of the liquid.2. Temperature of the LiquidConsider the temperature of the liquid you will be transferring. Screw pumps are suitable for liquid temperatures of up to 350 degrees Celsius.3. Characteristics of the LiquidConsider the characteristics of the liquid you will be transferring. The physical characteristics of the liquid will impact the type of screw pump you choose.ConclusionScrew pumps are essential for many industries. They are versatile, efficient, and cost-effective, making them the perfect solution for moving liquids of various viscosities. When selecting a screw pump, it's essential to choose an experienced and reputable manufacturer to ensure that you get the desired results.
How to Maintain Your Pump's Lube Oil System for Optimum Performance
Lube Oil System for Pumps Improves Operational Efficiency With the global demand for energy constantly on the rise, the oil and gas industry has been working towards improving operational efficiency and reducing costs. One critical area that has been identified is the upkeep and maintenance of industrial pumps, which play a vital role in the production and distribution of various types of fuels. To address this issue, a leading provider of pump systems and solutions has launched a new lube oil system that promises to revolutionize the way pumps are maintained and serviced.The lube oil system, developed by [company name], is designed to offer a complete solution for the lubrication and cooling of industrial pumps. It provides a reliable and consistent supply of oil to critical pump components, ensuring their proper functioning and longevity. The system features a compact design that makes it easy to install and maintain, with minimal downtime and disruption to operations.One of the key benefits of the lube oil system is its ability to provide accurate and real-time monitoring of pump performance. The system is equipped with sensors that measure oil pressure, temperature, and flow rate, allowing operators to detect any issues or abnormalities in pump operation. This proactive approach to maintenance can help prevent costly downtime and repairs, while also optimizing the performance and longevity of the pump.In addition to its monitoring capabilities, the lube oil system is also designed for easy maintenance and service. The system's modular design allows for easy access to critical components, making it simple to replace parts or perform routine maintenance tasks. This, in turn, reduces the need for specialized technical expertise and training, further reducing costs and improving efficiency.The lube oil system is compatible with a wide range of industrial pumps, including centrifugal, positive displacement, and reciprocating pumps. It can be customized to meet the specific needs of different pump applications, including offshore drilling, refining, and transportation. This versatility means that the system can be used across a wide range of industries, making it a valuable investment for any company looking to improve pump performance and reduce maintenance costs.Commenting on the launch of the new lube oil system, [company name]'s CEO said, "We are proud to introduce this innovative solution to the market. Our team has worked tirelessly to develop a lube oil system that delivers real value to our customers. We believe that this system will help our customers achieve better operational efficiency, reduce maintenance costs, and minimize downtime. Ultimately, our goal is to help our customers succeed, and we believe that this system will play a key role in achieving that."Overall, the lube oil system for pumps offered by [company name] is a game-changer for the oil and gas industry. Its ability to provide real-time monitoring, easy maintenance, and compatibility with various pump types makes it an ideal solution for companies looking to optimize pump performance and reduce maintenance costs. With this system, operators can focus on their core business operations, while relying on the lube oil system to keep their pumps running smoothly and efficiently.
Understanding How Triple Screw Pumps Work for Efficient Fluid Transfer
Triple Screw Pump Working - A Revolutionary Solution for Fluid TransferFluid transfer is an integral part of many industrial processes, ranging from oil and gas drilling to food processing. It's crucial to have efficient and reliable pumps that can handle a wide range of fluids, from low-viscosity liquids to high-viscosity slurries. In recent years, triple screw pumps have emerged as a revolutionary solution for fluid transfer applications, offering significant advantages over traditional pumping technologies.Triple screw pumps work on the principle of positive displacement, which means that a fixed amount of fluid is transferred with every rotation of the pumping elements. Unlike centrifugal pumps that rely on impellers to move fluids, triple screw pumps use three screw-shaped rotors - a driving screw and two driven screws - that mesh together inside a tight-fitting casing. As the screws rotate, they create a series of chambers that progressively enlarge and then shrink, resulting in a pumping action that moves the fluid along the casing.The unique design of triple screw pumps provides several benefits over traditional pumping technologies. Firstly, they can handle a wide range of fluids, from low-viscosity liquids like water and gasoline to high-viscosity products like heavy crude oil and asphalt. This versatility makes them ideal for use in various applications, including chemical processing, marine, power generation, and oil and gas production.Secondly, triple screw pumps offer reliable and consistent flow rates, even under high pressure or variable flow conditions. Their positive displacement nature means that the flow rate is directly proportional to the pumping speed, making it easy to control and adjust as needed. They are also virtually pulse-free, which reduces the risk of damage to pipelines, valves, and other downstream equipment.Lastly, triple screw pumps are highly efficient, with low power consumption and minimal maintenance requirements. The screws rotate at a low speed, which reduces the wear and tear on the components and extends the lifespan of the pump. Additionally, their compact design and simple construction make them easy to install and operate, saving time and costs.One company that has been at the forefront of triple screw pump technology is {remove brand name}, a leading manufacturer of industrial pumps and systems. Their triple screw pumps have been widely adopted in various industries, including oil and gas production, chemical processing, and food and beverage.{Remove brand name} triple screw pumps are specifically designed to handle high-viscosity fluids, making them an ideal solution for applications such as crude oil transfer, bitumen injection, and heavy fuel oil circulation. Their pumps can handle fluids with viscosities up to 60,000 cSt, which is significantly higher than other pumping technologies. This means that they can move highly viscous fluids without the need for heating or dilution, which can be costly and time-consuming.One of the key benefits of {remove brand name} triple screw pumps is their patented HSN technology, which stands for High-Speed Nitriding. This technology involves nitriding the screws' surface to create a hard, wear-resistant surface layer that reduces friction and extends the pump's lifespan. This results in lower maintenance costs and longer service intervals, which translates into higher uptime and lower overall operating costs.In conclusion, triple screw pumps are a game-changer in the world of fluid transfer, offering significant advantages over traditional pumping technologies. Their versatility, reliability, and efficiency make them ideal for use in various industries and applications, and their low maintenance requirements and robust construction ensure long-lasting performance. As a leading manufacturer of triple screw pumps, {remove brand name} continues to innovate and refine its technology, providing customers with the best possible solution for their fluid transfer needs.
Innovative Triple Screw Pump Technology: Revolutionizing Industrial Fluid Transfer
Triple Screw Pump Offers High-Level Performance for Industrial Applications{Company Name} is proud to introduce the triple screw pump, a high-level performance solution for industrial applications. With the ability to handle viscous fluids while providing smooth and continuous flow, this reliable pump is ideal for a variety of industrial processes.One of the significant advantages of this pump is its high efficiency. It can achieve up to 90% efficiency while still being able to handle high-viscosity fluids such as crude oil, asphalt, and bitumen. This makes it an ideal solution for industries that require a high level of performance in their fluid handling processes.Another key feature of the triple screw pump is its ability to maintain consistent flow, even with varying inlet pressures. The screw design creates a clearing action within the pump, which means that there is a minimal risk of clogging or blockages, even with thicker fluids.The triple screw pump has been designed with ease of use in mind, making it an ideal choice for operators who need a low-maintenance solution. A self-priming design enables the pump to start and stop without the need for manual intervention, and it requires minimal disassembly for cleaning and servicing.Moreover, the pump has a compact footprint, which makes it easy to install and integrate into existing systems. Its low noise and vibration levels make it an ideal solution for applications where noise pollution and vibration could be an issue.It is recommended for industries that deal with liquid transfer, applications that need high pressure, high viscosity, and high temperature. Additionally, the triple screw pump is ideal for applications that involve feeding multiple points at once, as it can operate on a different number of pressures and flows.Furthermore, the triple screw pump is highly customizable, which means that it can be tailored to meet the specific needs of individual applications. Customization options include different materials of construction, various sealing systems, and different RPMs to suit the application's requirements.{Company Name} CEO, {Name}, stated "We are thrilled to offer this high-performance solution to our customers. The triple screw pump is an ideal choice for industries that require consistency and reliability in their fluid handling processes."In conclusion, the Triple Screw Pump offers high-level performance for industrial applications. With its high efficiency, consistent flow, low maintenance requirement, and customizable design, it is ideal for industries that deal with high-pressure, high-viscosity, and high-temperature applications. Operators can use it to feed multiple points at once while achieving a smooth and continuous flow.
How Screw Pumps Increase Pressure in Industrial Applications
Title: Innovative Screw Pump Pressure System Reimagines Fluid Conveyance in Industrial ApplicationsIntroduction (124 words):With rapid advancements in industrial technology, the demand for efficient fluid conveyance systems has become more crucial than ever. Recognizing this need, innovative engineering company [Company Name] has unveiled their latest solution—an advanced Screw Pump Pressure System. Boasting remarkable reliability, versatility, and industry-leading performance, this cutting-edge system is set to revolutionize fluid conveyance across various industries. Designed with state-of-the-art technologies and engineering expertise, the [Company Name]'s Screw Pump Pressure System is a game-changer in terms of operational cost-efficiency, maintenance, and overall productivity. Let us delve into the remarkable features and benefits of this groundbreaking solution.Title: Enhanced Reliability and Durability(136 words)The Screw Pump Pressure System, developed by [Company Name], is engineered to deliver enhanced reliability and durability in industrial fluid conveyance operations. Through thorough research and rigorous testing, this revolutionary system has proven itself capable of withstanding high-pressure and high-viscosity fluid transportation. Utilizing advanced materials and cutting-edge engineering techniques, the system is built to withstand demanding industrial environments, minimizing downtime and increasing overall productivity.Designed with precision components and assembled with meticulous attention to detail, the Screw Pump Pressure System offers unparalleled performance and durability. From challenging offshore oil drilling operations to intricate chemical processing, this system can handle a wide range of demanding tasks, ensuring smooth fluid conveyance even in the harshest conditions. Its robust design ensures long service life, reducing maintenance costs and maximizing uptime for businesses in need of reliable and high-performance fluid conveyance solutions.Title: Versatile Fluid Handling Capabilities(140 words)One of the key highlights of the Screw Pump Pressure System developed by [Company Name] is its remarkable versatility in handling various types of fluids. Whether it is crude oil, lubricants, chemicals, or other viscous substances, this system guarantees efficient and reliable conveyance. With its ability to maintain a consistent flow, the Screw Pump Pressure System ensures minimal pulsation, ensuring smooth operations in critical applications.Furthermore, this innovative solution offers adjustable speeds and pressure capabilities, allowing for increased flexibility in meeting diverse industrial requirements. By adapting to a wide range of fluid viscosities, the system can seamlessly integrate into various production processes, significantly improving overall operational efficiency. This adaptability extends to both horizontal and vertical fluid conveyance applications, making it a versatile choice for a wide range of industries, including oil and gas, chemical processing, wastewater treatment, and more.Title: Unrivaled Performance and Cost Efficiency(140 words)The Screw Pump Pressure System developed by [Company Name] has set new benchmarks in terms of performance and cost efficiency. Equipped with precision-engineered screw rotors and advanced sealing technologies, this system ensures consistent flow rates, minimal leakage, reduced energy consumption, and optimal operational efficiency.Thanks to its exceptional performance, the Screw Pump Pressure System boasts significant cost-saving advantages for businesses in the long run. Reduced energy consumption translates to lower operational costs, while the system's low-maintenance design minimizes downtime, boosts overall productivity, and improves return on investment. Moreover, the enhanced performance capabilities of this system enable businesses to optimize their manufacturing processes, achieve faster turnaround times, and meet increasing production demands.Conclusion (112 words):In conclusion, the Screw Pump Pressure System developed by [Company Name] presents a transformative solution to fluid conveyance challenges in various industries. Its remarkable reliability, versatile fluid handling capabilities, and unrivaled performance and cost efficiency set it apart from traditional systems. With its ability to withstand demanding environments and handle diverse fluid viscosities, this system is poised to revolutionize fluid conveyance operations, driving industrial productivity and profitability. [Company Name]'s commitment to innovation and advanced engineering exemplifies their dedication to providing cutting-edge solutions that cater to the evolving needs of modern industries.
Innovative Centrifugal Screw Pump Technology Revolutionizing Industrial Pumping Applications
Centrifugal Screw Pump Proves to be a Game-Changer in Industrial ApplicationsIn the world of industrial applications, finding the right kind of machinery that suits the needs of the business is essential. Centrifugal Screw Pumps, also known as twin-screw pumps, have been creating waves in various industries lately. They have gained immense popularity due to their unmatched efficiency, versatility, and durability.A centrifugal screw pump is a positive displacement pump that transfers fluid by moving it through closely-spaced screws, generating pressure and flow. This particular pump's design enables it to handle tough-to-pump fluids with high viscosity and solids content. Consequently, the centrifugal screw pump is known to reduce maintenance costs, increase the lifecycle of machines, and enhance overall operational efficiency.However, the centrifugal screw pump by a prominent brand has gained significant attention for its cutting-edge technology, exceptional performance, and outstanding customer service. This high-quality pump has been used in several industries and applications such as marine, food processing, wastewater treatment, biodiesel production, and more.One of the many advantages of the centrifugal screw pump is the considerable reduction in cavitation. When a pump experiences high-pressure changes, there could be areas of low pressure that lead to the formation of cavities or bubbles. With traditional pumps, cavitation would cause significant damage, resulting in increased maintenance costs. Installing a centrifugal screw pump substantially reduces this problem since the pump can handle a higher level of turbulence without the creation of cavities.Another crucial advantage of centrifugal screw pumps is their ability to handle fluids of varying viscosity. They operate with a wide range of viscosities, even as high as 200,000 centipoises, without the need for external pumps. This feature allows it to handle more challenging fluids such as crude oil, molasses, and syrup.This pump design also facilitates the transfer of fluids with high solid content. It is capable of transferring up to 40% blockage in its internal flow chambers without damaging the rotor or the stator. This pump design makes it ideal for transferring abrasive fluids or slurries and is a critical component in several waste treatment systems.Moreover, the centrifugal screw pump is also suitable for metering applications due to its precise flow rate. Its discharge rate is unaffected by variations in fluid viscosity, temperature, or pressure, which is uncommon in other types of pumps. This accuracy makes it an ideal solution for transferring critical fluids in the pharmaceutical and chemical industries.Overall, this high-end centrifugal screw pump equipped with state-of-the-art technology is a guaranteed game-changer in the industrial manufacturing sector. \This pump has already made a significant impact in the industry by delivering unmatched performance and efficiency. With its ability to handle complex fluids, reduce maintenance costs, increase machine longevity, and improve overall operational efficacy, it remains the top choice for many businesses.Additionally, the company that produces this innovative centrifugal screw pump takes pride in providing customers with the best service in the industry. Their team of experts makes every effort to assist and guide clients in the selection, installation, and maintenance of equipment. They also offer comprehensive training to ensure maximum productivity and efficiency from the pump.In conclusion, investing in a centrifugal screw pump from this reputable brand is the best decision any business can make. It delivers exceptional performance, reduces production costs, and adds value to the entire manufacturing process. With its unmatched versatility and durability, it is the ultimate solution to all your fluid transfer needs. Contact their team today and experience the revolution in industrial manufacturing!
Understanding the Purpose and Function of Check Valves in Plumbing Systems
Check Valves: Supporting Fluid Control in Diverse Industries Check valves play an essential role in fluid control systems of various industries. A check valve, also known as a one-way valve or non-return valve, ensures the flow of fluid in a single direction. The valve automatically closes when the flow tries to reverse, preventing backflow and protecting pumps, compressors, and other system components from damage. Check valves can be found in different types, sizes, materials, and configurations to accommodate the specific requirements of different applications. They can be classified based on their design, such as swing, lift, ball, disc, piston, or diaphragm check valves. They can also be classified based on their application, such as in-line, wafer, flanged, threaded, or soldered check valves. Check valves can be made of various materials, including brass, stainless steel, PVC, titanium, and others, depending on factors such as the fluid type, temperature, pressure, and environment. Check valves find applications in many industries that handle fluids or gases, such as oil and gas, water and wastewater, chemical, pharmaceutical, food and beverage, power generation, marine, and HVAC. For example, check valves prevent backflow in pipelines that transport oil or gas, reducing the risk of contamination and avoiding the loss of valuable resources. In water and wastewater treatment systems, check valves prevent reverse flow that could damage pumps or inject chemicals into the wrong tanks. In the chemical industry, check valves ensure the proper flow of corrosive or hazardous fluids, preventing leaks or explosions. In the food and beverage industry, check valves maintain the quality and hygiene of the products by preventing cross-contamination. In power generation plants, check valves protect boilers, turbines, and heat exchangers from damage caused by steam or water backflow. In marine applications, check valves prevent seawater from entering the ship or offshore platforms, avoiding corrosion and environmental hazards. In HVAC systems, check valves ensure the proper circulation of air or water, reducing energy waste and improving comfort. One of the leading companies that offer check valves is a trusted manufacturer with a worldwide reputation for quality and innovation. The company has been in the business of fluid control products for more than a century, providing a wide range of valves, regulators, and fittings for various industries. The company's check valves are designed and manufactured to meet the highest standards of performance, safety, and reliability, and are certified by international organizations such as ISO, API, and ASME. The company's check valves incorporate advanced features that enhance their functionality and durability. Some of these features include: - Silent operation: The company's check valves use a spring-loaded disc mechanism that allows for silent operation, avoiding the slamming noise that other types of check valves can make. The check valves also have a low cracking pressure, meaning that they open with minimal pressure from the downstream fluid, ensuring that the system starts smoothly. - Easy maintenance: The company's check valves are designed for easy disassembly and cleaning, allowing for quick and hassle-free maintenance. The check valves have a threaded bonnet that can be removed without special tools, and the internals can be accessed and removed easily. - High flow capacity: The company's check valves are engineered to provide high flow capacity with low pressure drop, allowing for efficient fluid transfer and reducing energy consumption. The check valves have a streamlined flow path that minimizes turbulence and erosion, extending the valve's lifespan and reducing the risk of leakage. - Wide compatibility: The company's check valves are compatible with a wide range of fluids, including corrosive, abrasive, and high-temperature ones. The check valves can also handle different pressures, from low to high, depending on the application. The company offers check valves in various configurations, such as swing, lift, and ball check valves, and in different materials, such as bronze, stainless steel, and PVC. Some of the company's check valves are designed for specific applications, such as its double-door foot valve for well water systems, its sanitary ball check valve for food and beverage processing, and its high-pressure lift check valve for oil and gas pipelines. Customers can count on the company's technical expertise and customer support to choose the right check valve for their specific needs. The company's engineers provide customized solutions for complex fluid control challenges, and its customer service team offers prompt and efficient assistance for any inquiries, orders, or after-sales needs. In conclusion, check valves are vital components of fluid control systems in diverse industries. They provide essential protection against backflow, ensuring the safe and efficient operation of pumps, compressors, and other equipment. The company's check valves combine advanced features, high-quality materials, and expert engineering to deliver superior performance and reliability in different applications. With its global presence and customer-oriented approach, the company is a trusted partner for fluid control solutions.
Ultimate Guide to Industrial Marine Pumps: Uncovering the Top Solutions for Efficient Operations
[Assistant]Title: Leading Industrial Pump Manufacturer Expands Product Line to Meet Growing DemandSubtitle: Company showcases advanced solutions aimed at revolutionizing industrial marine applications [Introduction]In today’s rapidly evolving industrial landscape, the demand for efficient and reliable industrial marine pumps has reached unprecedented heights. Recognizing this, one of the industry's leading manufacturers has recently expanded its product line to cater to the needs of this niche market. This move aims to revolutionize the way industries approach marine applications, promising enhanced performance, reduced downtime, and improved sustainability.[Company Background]With decades of experience in pump manufacturing, the company has established itself as a trusted global leader in the industry. Known for its commitment to innovation and cutting-edge technology, the company has garnered a robust reputation within various sectors, including marine, oil and gas, power generation, and chemical processing.Driven by a passion for continuous improvement, the company invests heavily in research and development to ensure the highest quality products are offered to its customers. As a result, they boast an extensive portfolio of efficient, durable, and cost-effective solutions that have become synonymous with excellence.[Diverse Product Range]Expanding on their range of industrial pumps, the company has launched an array of advanced marine pumps, specifically designed to withstand the harsh operating conditions encountered in marine environments. These pumps offer a wide range of applications, including ballast water management, cargo handling, bilge pumping, cooling systems, and more. The company's commitment to meeting the unique demands of the marine industry is evident through the latest product offerings.1. Cutting-edge Ballast Water Management Systems: Recognizing the significance of environmental conservation, the company has developed highly efficient ballast water management systems that comply with international guidelines. With advanced filtration and disinfection technologies, these systems ensure the prevention of invasive species transfer without compromising vessel performance.2. Cargo and Bilge Pumps: Engineered to handle the demanding requirements of cargo handling and bilge pumping, the company's pumps deliver exceptional reliability and operational efficiency. With features like high flow rates, corrosion resistance, and low maintenance requirements, these pumps stand as a testament to the company's commitment to delivering long-lasting and highly effective solutions.3. Cooling Systems: Marine vessels mandate reliable cooling systems to maintain optimal operating temperatures. Understanding this critical need, the company offers an extensive range of cooling pumps designed to withstand the unpredictable conditions encountered at sea. Notable features include compatibility with both fresh and seawater, efficient heat transfer capabilities, and high corrosion resistance.[Innovation and Sustainability]Priding itself on being an industry pioneer, the company continuously strives to develop sustainable solutions to minimize environmental impact. The introduction of eco-friendly materials, energy-efficient systems, and technologies that reduce carbon emissions further reinforces their commitment to sustainability.To enhance operational efficiency, the company has incorporated smart monitoring technologies into their marine pumps. Real-time data monitoring and predictive maintenance capabilities ensure optimal performance, reduced downtime, and cost-effective operations.[Future Prospects]With their expanded marine pumps portfolio, the company is well-positioned to cater to the rapidly growing industrial marine sector. As the demand for efficient water management, cargo handling, and cooling systems continue to rise, the company's advanced solutions are set to play a pivotal role in transforming the industry.To further support their customers, the company has bolstered its after-sales services, ensuring timely maintenance, spare parts availability, and a dedicated support team to cater to any queries or concerns. These customer-centric initiatives reinforce the company's commitment to delivering holistic and reliable solutions to clients worldwide.In conclusion, the recent expansion of industrial marine pumps by the leading pump manufacturer demonstrates their dedication to meeting the requirements of this rapidly expanding market. With innovative technologies, sustainable practices, and a commitment to customer satisfaction, the company aims to revolutionize the industrial marine industry, setting new benchmarks for efficiency, reliability, and environmental responsibility.
Discover the Distinctions Between Screw Pumps and Gear Pumps
Screw Pump and Gear Pump: Understanding the Differences in Pumping TechnologyPumping technology plays a crucial role in various industries, from manufacturing and oil and gas to wastewater treatment and food processing. For efficient and reliable pumping, two types of pumps that are often utilized are screw pumps and gear pumps. While both serve the purpose of moving fluids from one place to another, they differ in design and application. In this article, we will explore the differences between screw pumps and gear pumps.A screw pump, as the name suggests, operates by using rotating screws to move fluids from the inlet to the outlet. It consists of two or more intermeshing screws contained within a cylindrical or semi-cylindrical housing. The screws rotate in opposite directions, trapping the fluid between them and forcing it to move along the length of the screws. This type of pump is known for its gentle and smooth operation, making it ideal for handling shear-sensitive fluids or those containing small solids.On the other hand, a gear pump works by using two or more intermeshing gears to create a pumping action. The gears rotate in opposite directions, creating a partial vacuum at the inlet, which draws the fluid in, and then forces it out through the outlet. Gear pumps are characterized by their simplicity, compactness, and high-speed operation. They are commonly used for high-pressure applications, such as hydraulic systems, and for handling clean fluids with low viscosity.The key difference between these two types of pumps lies in their design and how they move fluids. Screw pumps use the rotating action of the screws to transport the fluid, while gear pumps rely on the intermeshing gears to create the necessary pumping action. This fundamental distinction affects the overall performance, efficiency, and suitability of each pump for specific applications.In terms of performance, screw pumps are known for their ability to handle viscous fluids and those with solids content. The continuous and smooth motion of the screws ensures minimal pulsations and provides a steady flow, making it suitable for applications where a consistent output is required. On the other hand, gear pumps excel in generating high-pressure output, making them ideal for applications that require pressurized fluid delivery. Their precise metering capabilities also make them suitable for applications that demand accurate flow control.When it comes to efficiency, screw pumps offer higher volumetric efficiencies compared to gear pumps. Due to their progressive cavity design, screw pumps can handle variable flow rates with minimal slip, ensuring a higher percentage of fluid is efficiently moved from the inlet to the outlet. Gear pumps, while generally less efficient, compensate with their compact size and ability to generate high pressure, making them suitable for space-constrained environments or applications with specific pressure requirements.In terms of application, screw pumps find extensive use in industries such as wastewater treatment, oil and gas, chemical processing, and food manufacturing. Their ability to handle high viscosity fluids, such as sludge, oil, and syrup, makes them suitable for these demanding environments. Gear pumps, on the other hand, are commonly employed in hydraulic systems, fuel transfer, lubrication systems, and various industrial processes that require high pressure and precise flow control.In conclusion, screw pumps and gear pumps are two distinct types of pumping technology, each with its own benefits and applications. Screw pumps offer gentle and steady fluid movement, making them well-suited for shear-sensitive fluids and those with solids content. Gear pumps, on the other hand, excel in generating high pressures and precise flow control, making them ideal for applications with specific pressure requirements. Understanding the differences between these two types of pumps can help industries make informed decisions when it comes to selecting the most suitable pumping technology for their specific needs.